Water Bore Pump Testing | Best Equipment Still Now
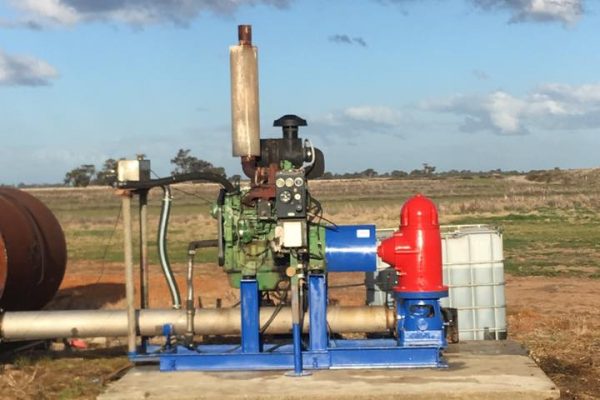
Water Bore Pump Testing is a method of evaluating water flow. It bases on observations of continuous water sources. And, it tells the presence of water from the source. Pumping tests entail pumping at a regulated pace from a test well. It measures the flow rate from the well.
Transmissivity, hydraulic conductivity, and storativity may consider some of the aquifer properties determined. The step drawdown test may use to assess the well’s performance. The coefficient of aquifer loss and well loss, efficiency, specific capacity, well development factor, and optimal pumping rate may assess.
Water Bore Pump Testing may use to measure conditions debits in a variety of ways, including:
- The difference between these two circumstances is 1. Then, source debit equals water debit pump discharge (pump output).
- The source debit may consider lower than the pump debit. So, the rate of water drop during pumping may become larger than the rate of water rise during recovery.
- The source debit may consider greater than the pump debit. The rate of reduction in surface water during pumping may consider less. Then, the rate of increase in surface water during recovery.
Information About Pumping Tests And A Disclaimer
Unless the contractor performs the genuine pumping tests using an actual submersible pump. The flow test may not deem accurate in the majority of situations. During the first few weeks of use, a water well’s flow frequently improves noticeably. Thus, the development of the well before it occurs in operation may and should speed up this progress. A pump test should perform once the well has been sufficiently developed or after a few weeks of use. So, this pump test will provide a considerably more accurate flow measurement than the driller’s original flow test.
Water Well Pumping Test Using Ultrasonic Flowmeter
For Water Bore Pump Testing, many employ an ultrasonic non-invasive flowmeter. This entails delivering and receiving ultrasonic pulses from a pair of sensors. And, it analyses the signal’s timing difference. This gadget works by using clamp-on transducers positioned on the pipe’s outside surface. And, it creates pulses that flow through the pipe wall. The timing variations in the ultrasonic signals may cause by the flowing liquid within. They may then analyses by the flowmeter. So, it generates an accurate flow measurement.
Read More: A HOMEOWNER’S GUIDE TO WELL WATER SYSTEMS.
Choosing A Submersible Pump
The original cost, installation cost, operation cost, maintenance, and estimated equipment life may consider all factors to consider for any pump. Proper component selection can assure system performance. It change conditions may need replacing or reselecting components to maintain cost-effective operation.
So, it guarantees dependable performance, the range of expected working circumstances. It includes ambient air and water temperature ranges, pressures, flow, corrosive and abrasive variables, power supply fluctuation, duty cycle, and protection devices. Thus, they may compare to the pump manufacturer’s specifications. So, the pump must fit following the manufacturer’s instructions.
Continuous pump operation may consider preferable to intermittent pump operation. It fluctuates water demand usually necessitates a combination of off and on time. System components and storage capacity should design to reduce pump starts. And, it stops per day for enhanced well performance and pump life.
At the same time, the pump must size and configured such that it never runs “any delivery” for more than a few minutes, as this will damage the pump bearings and cause the submersible motor to fail.
Pump protection should give if the good decline or delivery system causes the pump to run with little or no delivery.
A well-level switch, for example, may shut down the pump or sound an alarm if the flow or water level falls below a safe minimum level. Greasing bearings, polarity tests, and alignment checks are examples of routine maintenance that the manufacturer may provide.
The Following Are Important Aquifer Parameters
The vacant space in rock formations may measure by porosity. The ratio of the void pore zone to the total rock formation measured may be defined in percentages.
Hydraulic Conductivity
Flow rate over a unit cross-sectional area of an aquifer under a unit hydraulic gradient. The unit may measure in millimeters per day.
Transmissivity Rate Of Groundwater
Flow across an aquifer of unit breadth and thickness under a unit hydraulic gradient. Transmissivity is equivalent to the crop of hydraulic rods and aquifer breadth. The measurement is in m2/day.
The volume of water released from safety per unit surface zone of a confined aquifer per unit drop in the hydraulic head is called storativity or storage coefficient in confined aquifers. It has no dimensions.
The volume of moisture released from storage under gravity by an unconfined aquifer per unit surface area of aquifer per unit decreases the water table, applicable for unconfined aquifers. Specific yield is either dimensionless or expressed as a percentage.
In m3/hour/m, the specific capacity of a well is the ratio of the well’s discharge to the drawdown. The Water ACS Equip – bore services Pump Testing goals are to measure well yield, well efficiency, aquifer characteristics, and water chemistry. Pump testing is an important investigative technique. It necessitates careful planning, observation, and data interpretation.
If existing wells can use, it is substantially less expensive. Newly built wells are subjected to pumping tests. The space between you and the other human should not be too great.
Pumping Rate Regulation
During the test, it’s critical to keep the pumping rate under control. It enables the collection of accurate drawdown data to determine the well’s yield and aquifer parameters. Adjusting the pump speed to control the pumping rate is often ineffective. To maintain a steady pumping rate, it is preferable to employ a gate valve.
When pumping at the specified pace, the discharge pipe and valve should be sized so that the valve is open between 12 and 34 percent of the time. The valve should be positioned far enough away from the flow monitoring instrument to reduce turbulence effects. It’s also crucial to correctly measure the discharge of pumped water, and standard ways include using an orifice plate and a manometer.