HOW TO REDUCE NON-QUALITY COSTS IN YOUR COMPANY
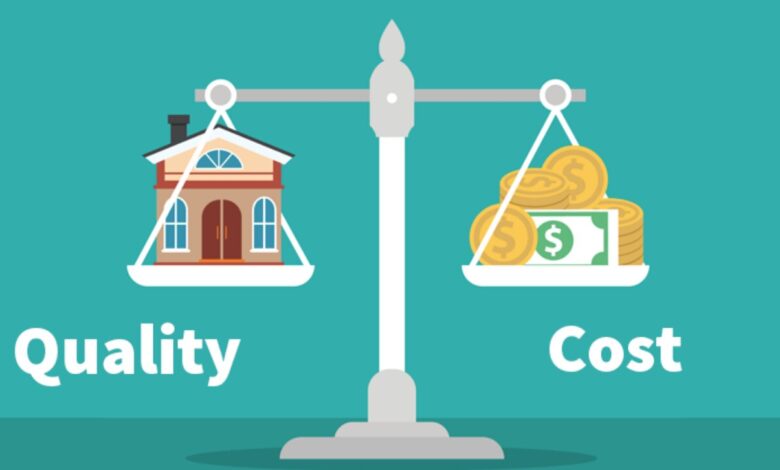
One of the challenges for any furniture or upholstery manufacturer is lowering non-quality costs.
When we take steps to identify and reduce these types of costs, our company can achieve better results.
What are non-quality costs in a furniture factory or company? We are going to explain it to you in this post, and also what tools you need to monitor your production and increase your profitability.
NON-QUALITY COSTS: WHAT THEY ARE AND WHY THEY MATTER
Non-quality costs are a key concept in the quality management of a company. In English, they are known as Non-Quality Cost, although there is another similar concept called Cost of Poor Quality (COPQ), which would be the costs derived from units of little or low quality. In short, these are all those costs derived from not having managed to meet the customer’s requirements.
For example, if in a furniture sales company, the customer returns the product because it has manufacturing defects, re-manufacturing the same furniture or repairing any damage it may have will entail an extra cost. Those would be the non-quality costs, since what they are doing to decrease your profit margin or even make you lose money if you have to re-manufacture the item.
The non – quality costs are important because the higher they are, the less you are getting the benefit. Your quality control processes can be improved and your customers are complaining. Therefore, a high percentage of non-quality costs is a bad indicator.
To reduce these costs, one of the possible strategies is to increase your quality costs. That is, invest in processes, production control software, and quality control systems to reduce defective units.
HOW TO REDUCE NON-QUALITY COSTS?
The answer is very obvious; what you should do is optimize your production processes to the maximum.
You must avoid errors, reducing the number of defective units produced. It is also necessary to better control manufacturing orders, assigning tasks to employees, and managing productivity.
Find out where manufacturing faults or defects occur. For that, a solution like SIM. The camera view could be of great help. It is a tool to inspect the objects before they are packed and shipped to the customer. In this way, you make sure that you do not send defective products.
WHAT AREAS OF YOUR BUSINESS CAN NON-QUALITY COSTS AFFECT?
The non – quality costs can not only be present in the manufacturing process. They can be related to other phases of the sales process. For example, in logistics management. If the units produced to break down on the way in the transport vehicle, the problem is the logistics management and not the manufacturing process.
In a furniture company or the rest sector, these costs can also be present in the sales process. If too many mistakes are made when taking note of customer specifications, products can be made on-demand with the wrong requirements.
Here the problem is in the commercial service and the attention to the client. A 3D simulator that allows you to send the data directly to the factory would help solve many problems.
By reducing the problems of non-quality costs, you will have more satisfied customers, your brand will be more valued and you will be able to obtain a greater profit.
Looking for a Ribbon blender mixer manufacturer in Ankleshwar? Stalwart International is the best option for you.