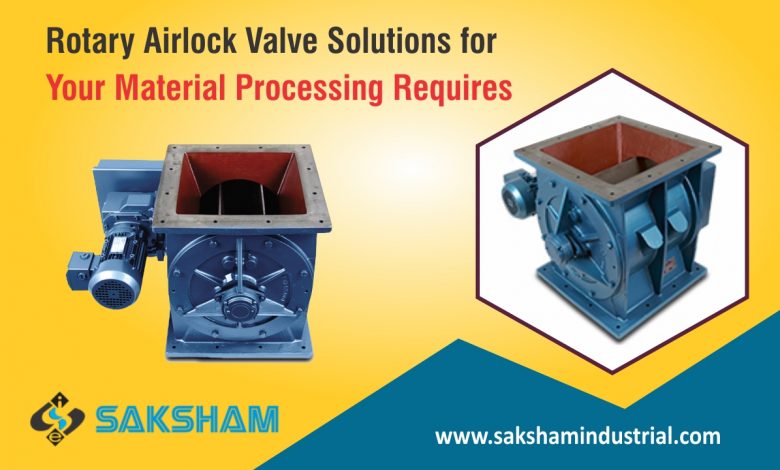
A Rotary airlock valves are important for your dry bulk material handling as well as pneumatic conveying systems to run securely and efficiently. Rotary Airlock Valves, also known as Rotary Airlocks Rotary feeders, rotary valves, and countless other variations. Control the flow of and a range of material from one chamber to the next whereas preventing air leakage. In addition to controlling the flow of material, rotary valves are also very important safety mechanisms acting as a flame barrier in the event of a dangerous dust explosion.
Why Choose An Industrial Rotary Airlock Valve From SAKSHAM?
SAKSHAM understands that rotary airlock valves play a vital role in the performance of your bulk material handling as well as pneumatic conveying systems. Moreover, choosing the right rotary airlock valve is key to maintaining a production and dependable plant operation. We delight ourselves on the attention we give every valve that leaves our shop.
However, our many years of experience in the design of both dust collection as well as pneumatic conveying systems, and, the design and manufacture of rotary airlock valves, provides us with the engineering know-how to comprehend which kinds of rotary valves will best meet your airlock and feeder requirements. We make it our main concern to understand your processes and your applications. Thus, we can confidently advise the right solution that best addresses your material processing needs whether it be a new valve or the need to renovate and repair & existing valve.
Features and Benefits of Our Rotary Airlock Valves & Feeders
- Various designs provide options to addressing your specific needs.
- Cast iron construction offers a rugged design if the greatest structural stability.
- Precision-machined housing reduces rotor-to-barrel clearances, limiting leakage.
- The Outboard bearing design protects bearings from contaminates that extend maintenance cycles.
- Packing gland type seal makes for easy maintenance saving on costs.
- Open throat valve inlet design make sure material flows to rotor packets maximizing performance.
- Moreover, It handles pressure differentials up to 15 psi making it well suitable for pneumatic conveying operations.
- Chain and sprocket driven provides a smaller footprint and greater speed assortment providing flexibility to the applications used in your process.
Key Considerations for Rotary Airlock Valve Selection
Choosing the correct Rotary Airlock Valve for your dry bulk material handling & pneumatic conveying systems is important. Moreover, Numerous key considerations need to be taken into account when selecting rotary airlock valves.
The Type of bulk material thing processed
- Type of application
- Operating temperature
- Resistance Level of abrasion required
- Material density as well as moisture levels
Size and Valve Design Considerations
Selecting the correct valve size and design is critical to running your feeding as well as metering systems safely and efficiently while minimizing pressure loss. When choosing your valve, consider the following:
- If clearances are not set properly, air can leak through the valves. Air loss through the valve can help to –
- Reduce the volume of the feed rate capacity,
- Create unstable flow conditions,
- Create blockages in conveying line and
- Cause extreme wear on the interior surfaces.
However, Pressure, rotor clearances and material properties are all contributing factors to the quantity of rotary valve leakage.
- Maintaining a constant vacuum or air pressure differential between the inlet as well as outlet ports. While continuously moving material is essential to proper functioning of rotary valve.
- For abrasive applications, hard chrome interior surfaces are required.
- Open end rotors are usually used for abrasive materials. However, with open end rotor design, the material meets the housing bore also the inside surfaces of both end plates.
- Closed end rotors used to handle the pellets. In a closed ending rotor design, the only area of the blade affected is the blade tip adjacent to the housing bore. The end of the house pastes are not affected.
Rotary Airlock Valves, also known as Rotary Airlocks Rotary feeders, rotary valves, and countless other variations. Control the flow of and a range of material from one chamber to the next whereas preventing air leakage. In addition to controlling the flow of material, rotary valves are also very important safety mechanisms acting as a flame barrier in the event of a dangerous dust explosion.
We “SAKSHAM” a leading Rotary Airlock Valves Manufacturers, suppliers and exporters in India. However, we object on the design and manufacture of custom-made rotary airlock products which will rapidly get better the protection, reliability, and efficiency of your feed and measurement metrics compared to different rotary valve brands.
Not sure what type or size of rotary airlock valve you require. Ask our experts. We are here to help!